Timber industry struggling after burst housing bubble
Go Deeper.
Create an account or log in to save stories.
Like this?
Thanks for liking this story! We have added it to a list of your favorite stories.
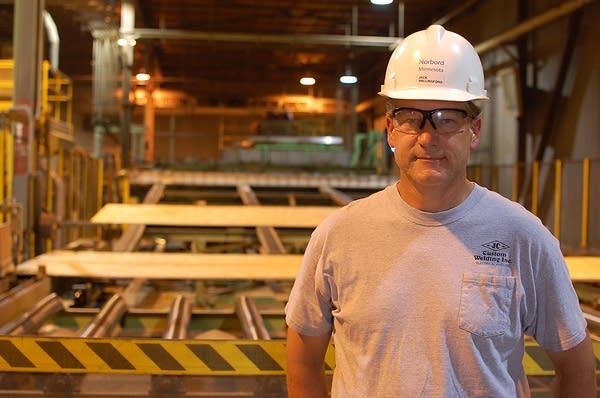
A few years ago, the Norbord Minnesota plant west of Bemidji was one of four plants in northern Minnesota making a plywood-like product called oriented strand board. Now Norbord is the only plant still running.
Since new home construction started to tank in 2007, the company has tried to keep its doors open and maintain jobs for about 140 employees, and provide work for loggers and haulers, said Jack Wallingford, the plant's general manager.
"We've been successful in that regard," he said. "Past that, it's been a rough stretch."
Although timber is a $17 billion dollar industry in Minnesota, an anemic housing market has put segments of that industry on life support. Thousands who depend on timber for their livelihood have lost their jobs. Plants and mills have shut down.
Turn Up Your Support
MPR News helps you turn down the noise and build shared understanding. Turn up your support for this public resource and keep trusted journalism accessible to all.
Timber related businesses that survived the economic shake-up are hanging on, waiting for a recovery. But economists say that could be years away.
Until a rebound occurs, times will be tough for any business tied to housing. That includes wood floor manufacturers and producers of board lumber, cabinets and windows. Wallingford said most companies that survived aren't making any money.
"There's been way more quarters we've lost money than what we've made," he said. "Since the bottom of the crash ... we've had very few profitable quarters as a company."
Timber economists estimate Minnesota lost more than 5,000 timber- related jobs since the start of the recession, including about 600 logging and hauling jobs.
Rajala Companies, a wood products producer in Big Fork and Deer River, has trimmed its workforce from 300 to 70, vice president John Rajala said.
"We're in complete survival mode."
"It's horrible," he said. "It's just, we're in complete survival mode."
The family-owned company has survived by producing boards for the wood packaging industry and also by exporting some hardwoods to China. But it focuses on products marketed directly to local consumers, things like specialty wood flooring and maple tongue and groove ceilings.
The company is losing money, but with those new niche products, Rajala hopes it can stay afloat until new home construction picks up.
"Family owned, independent sawmills like ours in the lake states region [are] probably two-thirds gone, literally just gone, at least in terms of employment," he said. "In most cases just literally, they're bankrupt or there's been consolidation and closures."
There is a bright spot for the timber industry. Paper manufacturers like Boise in International Falls and UPM-Blandin in Grand Rapids are doing relatively well and managed to avoid job cuts. A recent report from the state Department of Natural Resources found that the state's paper industry rebounded more quickly from the recession.
"They've been running at pretty good capacity and pricing is strong," said Don Deckard, an economist with the department's forestry division. "We've seen some softening of prices in August, but it's still a profitable business right now."
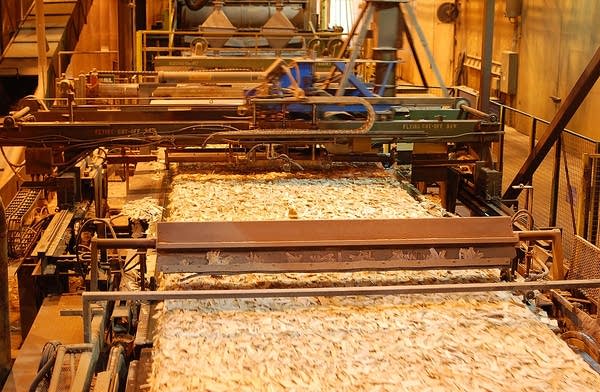
Low demand for raw timber from Minnesota forests has driven down prices. That's hurt private landowners, who've largely stopped selling timber. The state continues to sell cheap timber to support the industry, but it's meant a 20-percent drop in gross timber revenue for state coffers.
The future of the timber economy will likely include new technologies, including wood-based bio-fuels, bio-chemicals and bio-plastics. But Deckard said that while new bio-businesses in some states are getting big federal grants to develop those industries, that's not happening much in Minnesota.
"Wisconsin is getting it, Michigan is getting it. Ontario is getting it. But we're not," he said. "We're not getting anything. Nothing is moving. It's a very frustrating situation."
Deckard said the problem is that neighboring states offer more incentives for bio-businesses, including help with financing.
Experts say the real key to reviving the timber industry is a recovery in new home construction.
Homebuilding in the United States has dropped nearly 75 percent from a peak of about two million homes in 2005. Economists predict new housing starts won't hit the one million mark again until 2013.