Pay a sticking point for manufacturers seeking skilled workers
Go Deeper.
Create an account or log in to save stories.
Like this?
Thanks for liking this story! We have added it to a list of your favorite stories.
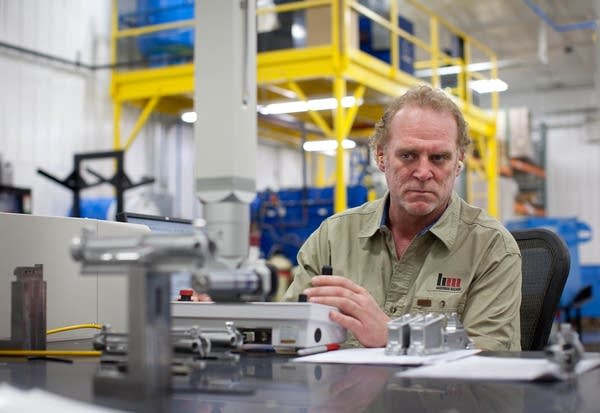
Haberman Machine's plant in Stillwater looks more futuristic than factory-like. Lined with white, boxy machines about the size of a closet, its machines cut stainless steel and aluminum into precisely shaped parts used in the oil, gas and defense industries.
Workers duck their heads in and out of the boxes to check their performance, but their jobs don't seem especially physical. In fact, they require a lot of brains. Several workers have received advanced training to program the computerized machines. That requires crack math skills.
"You need to have a skilled workforce to run these very expensive pieces of equipment — to set them up to run a part," said owner Scott Ness, a sales engineer.
His family has owned Haberman Machine since 1983.
Turn Up Your Support
MPR News helps you turn down the noise and build shared understanding. Turn up your support for this public resource and keep trusted journalism accessible to all.
Like a lot of manufacturers in Minnesota, Haberman is hiring. The openings include five positions for high-skilled machinist jobs that pay up to about $60,000 a year. But company officials haven't been able to fill the jobs and as a result haven't taken on the new business they need to grow.
View a chart on job vacancies and median hiring wages.
A recent survey of manufacturers across the United States found that as many as 600,000 jobs are vacant due to a shortage of skilled workers. The poll, conducted by Deloitte and The Manufacturing Institute, declared that factories are experiencing a moderate to severe shortage of qualified workers.
Schools like Dunwoody College of Technology in Minneapolis can't graduate students from their manufacturing programs fast enough to meet employers' hunger for talent. Last spring, several of the school's manufacturing training programs placed 100 percent of their students with employers.
In his State of the Union speech this week, President Barack Obama echoed that concern — a lament heard in factories across Minnesota.
"If you don't have the skilled workforce that can make quality parts over and over again, you lose your customer," Ness said.
The folks at Haberman Machine are so worried about the supply of workers that they were reluctant to share their workers' names. They fear other companies will try to lure them away.
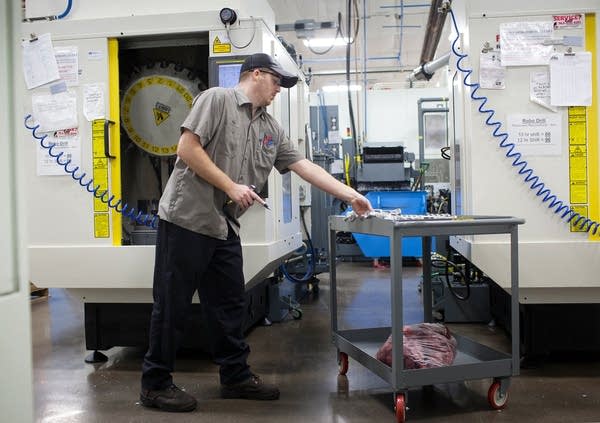
Among the workers the company recruited is Mike Beedle, a quality control technician.
Beedle, who has worked in manufacturing for 25 years, said he likes the company but is not crazy about his pay. He's still making about a third less than he did in a similar job at a medical device company that laid him off five years ago.
"If you want to know where I am with money, it's gone down a lot in the past few years," he said. "I'm not happy about that."
To Beedle, his declining wages suggest there is an oversupply of workers like him — not a shortage. So he doesn't totally understand manufacturers' gripes.
"They don't get the skilled workers they want, but they expect a lot," he said. "The more you pay, the better the worker you're going to get."
That makes sense to experts. Steve Hine, the state's head labor market analyst, said if skilled manufacturing workers were scarce, companies would have more job openings and offer higher wages.
"It seems that offering higher wages would be a natural response," Hine said.
With a labor shortage, out-state manufacturers who often have the toughest time filling positions would see a greater need to offer higher wages to attract workers, he said.
But that's not happening. The data on job openings for highly coveted machinists who can operate or program computerized machining tools doesn't show an unmet demand for such skills.
According to the most recent numbers, the median wage offer for such top machinists was $19 an hour. That's a healthy salary. But it's lower than the salary offered a few years ago, before the recession.
"If you go back to the fourth quarter of 2007, the median wage offering was $19.23, slightly higher, but nonetheless higher," Hine said. "So the wage offers in this area have fallen."
But the decline in wages is nothing like the huge drop in job openings for computer numerical control machinists. They've plunged about 70 percent from their peak four years ago.
That pattern repeats itself across other jobs, like welders.
Mechanical engineers, by contrast, have seen a rise in job vacancies. But wages for those workers have been stagnant since the start of the recession.
Hine said with vacancies and wages both dropping, he doesn't buy the argument that there is a worker shortage in the state.
Others say if manufacturers really do feel pinched for workers, they should provide more on-the-job training. Even many in the industry believe that's true.
"I'd really like to see more of the apprenticeship idea get into play," said Paul Huot, president of the Minnesota Precision Manufacturing Association. "Certain companies have rejuvenated that concept and they're doing internal training. And they're using the technical schools to help with the training. But I just think that we could do better."
But smaller firms find it tough to pay more and offer more training, said Jennifer Brigham, owner of Brigham Group Staffing.
Brigham's company works with a lot of mid-sized manufacturers that can't project their worker needs out very far.
For many companies, the general tentativeness of the economy has led to frequent last-minute orders. That makes it hard to invest in training workers, as a company's staffing needs may only be immediate, Brigham said.
Brigham said manufacturers can only raise wages so much. In part that's because manufacturers in Minnesota are competing to make their products better than those made overseas — where wages are much lower — but just as cheaply as those competitors.
That said, Brigham said high demand for skilled labor could drive wages up this year. She also expects to see companies' top talent seeking better pay elsewhere.
While Beedle isn't scoping out other gigs, he does understand the impulse to do so.
"That's business, capitalism at its finest," Beedle said. "If the company is in it for money, why can't the worker be in it for money?"
If wages don't rise, the complaints about a shortage of skilled workers may well continue.