Public-private partnership moves faster to supply skills
Go Deeper.
Create an account or log in to save stories.
Like this?
Thanks for liking this story! We have added it to a list of your favorite stories.
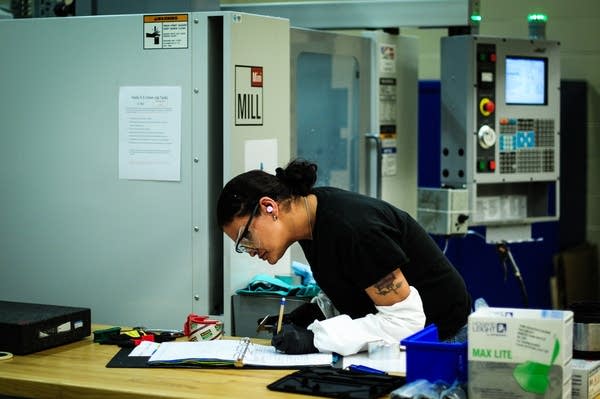
Six students in a classroom at Northwest Technical College are learning how to operate a big piece of factory equipment called a CNC machine. They're learning how to run the computer-aided machine to make metal parts, how to read blueprints and how to make fine measurements of what they produce.
None of them are actually enrolled in the college.
Instead, they are taking advantage of a public-private partnership that has created the Minnesota Innovation Institute to fill gaps in training and to connect people with jobs.
As the manufacturing industry moves into a post-recession hiring mode, some employers, particularly in rural Minnesota, have struggled to find workers with the right skills. The institute is one way employers and educators are trying share the burden and move more quickly by using private resources to address training needs.
Turn Up Your Support
MPR News helps you turn down the noise and build shared understanding. Turn up your support for this public resource and keep trusted journalism accessible to all.
"Good jobs up in this area are kind of scarce, hard to find, and I'm glad to be with this company."
The four men and two women in the Bemidji classroom are new employees of TEAM Industries, a Bagley-based manufacturer of all sorts of precision gears for vehicles. The students are getting paid by TEAM while they're getting trained.
"My foot is in the door," said Josh Medina, a 23-year-old Laporte resident who has some factory experience but not the skills needed for many manufacturing jobs today. "You always see these jobs in newspapers, but they want two to five years experience and a degree, so this gives it to you right here."
Once Medina and his classmates wrap up the two-week introductory course, paid for by TEAM Industries, they'll head to work at the company's manufacturing plants in Bagley and Park Rapids. In three to six months they'll come back for a second round of training.
Amber Elkhoderi, 48, of Akeley, started work at TEAM's Park Rapids plant four months ago as a temporary employee. That was her first exposure to CNC, or computer numerical control, machines.
Elkhoderi says the training will make her job permanent, and it puts her on a pathway where she can advance with the company as she gains more skills in the future.
"This means a lot to me," said Elkhoderi. "It's opened up a lot of doors. I think that good jobs up in this area are kind of scarce, hard to find, and I'm glad to be with this company."
TEAM Industries employs close to 900 people at its four plants in northern Minnesota. About 100 more work at a facility in North Carolina. TEAM and other manufacturers in the area often need specific training that is not offered by the technical college or by Bemidji State University, said company spokesman Jim Russ.
"We've had probably 10 companies come forward and say, 'I want in, I'll support you, I'll donate, I'll give cash.' This is being asked for. It's needed."
"This is new stuff," Russ said. "The last five to 10 years, the job skills that are presenting themselves have gaps. It's not easy for education to turn on a dime and help meet those needs. So that's a partnership thing. That's a leadership thing."
The partnership is among TEAM and a handful of other regional manufacturers, Northwest Technical College, Bemidji State, the Department of Employment and Economic Development and others.
It pools public and private resources to try to fill the skills gap. Bemidji State and Northwest Technical have contributed about $150,000 in seed money for the new program. TEAM Industries is paying for private trainers and donated training equipment.
The private trainers come from The Idea Circle, a Bemidji-based company that provides workforce organization, development and training for manufacturing and other industries.
Co-owner Robin Larson and her business partner, Mary Eaton, are both former customized trainers with Minnesota State Colleges and Universities. Though Bemidji State and Northwest Technical still offer customized training in the region, there is less focus on basic manufacturing skills than there was in years past.
Larson says the Minnesota Innovation Institute is an industry-driven effort, which helps her trainers tailor classroom and lab instruction to the needs of companies, which she says are lining up to participate.
"We've had probably 10 companies come forward and say, 'I want in, I'll support you, I'll donate, I'll give cash," said Larson. "This is being asked for. It's needed."
"I see an unemployment rate of about 8 percent and at the same time I'm hearing from companies that say they need people. It doesn't seem to make sense."
Russ said he and other manufacturers have been frustrated that state money designed to enhance manufacturing has typically not found its way to all parts of the state.
"There are limited funding streams now to go after," Russ said, "and largely those investments go to a few sheltered campuses near the Twin Cities. And because this is a larger issue than that, we need the Legislature, and we need agency commissioners, and we need the MNSCU chancellor's office to all be paying attention to allotments outside to Greater Minnesota."
Russ and others are also concerned that manufacturing-related offerings at Northwest Technical and Bemidji State are shrinking.
"I wish I could say that we've been able to sustain and grow programs, but as a matter of placement and record, both those institutions have gotten rid of programs," Russ said.
In fact, Bemidji State University eliminated two industrial tech degree programs in 2011 in response to steep state budget cuts. The university says those programs failed to attract enough students to be sustainable. The university still has three manufacturing-related degree programs with combined enrollment of about 250 students.
Northwest Technical College is phasing out its only degree program in manufacturing. Northwest Technical provost John Centko said even though graduates were able to find good jobs, that program suffered similar low enrollment problems.
Centko plans to refocus the college's efforts on a curriculum that meets the more immediate needs of industry. He wants a set of shorter, certificate-level courses that fill the gap in skills.
"Sometimes we aim at the target but we miss the point," Centko said. "We really need to align those skill sets a little bit differently and adapt much quicker."
Centko says he'll pay close attention to the pilot courses offered through the Minnesota Innovation Institute. He says those courses could someday become a permanent part of Northwest Technical's curriculum.
"Everybody holds part of the puzzle," Centko said. "But how to put that puzzle all together into a pipeline that makes it be able to move efficiently and effectively, that's an art. And that takes all of the resources coming together."
Public-private partnerships like the Minnesota Innovation Institute seem likely to become more common. Mary Rothchild, senior system director of workforce development for Minnesota Colleges and Universities, said schools aren't always able to put needed programs in everyone's back yard, but it helps to work directly with industry.
"Within reason, we should be able to come up with solutions to meet the needs of employers," Rothchild said "If we can help our employers grow their businesses by providing local solutions, we should try."
The Minnesota Innovation Institute is looking for a permanent home, said Dave Hengel, director of an economic development organization called Greater Bemidji, another institute partner.
The goal is to find a building that can serve as a training and consulting center for manufacturing, and also a space for state agencies that focus on job skills. That will likely include DEED, which would play a greater role in providing career and aptitude assessments for job candidates.
"I sit here as the economic develpment director for the region and I see an unemployment rate of about 8 percent and about 1,600 people actively seeking employment," Hengel said. "At the same time I'm hearing from companies that say they need people. And it doesn't seem to make sense, and so there's a disconnect there that we're trying to figure out.
"Economic development has really become a race for talent more than it is a race for companies," he said. "And so the extent to which I can churn out high end skills that are in demand for companies, the more likely the Bemidji region will be looked at for a place to own and operate a business."