Scale of PolyMet technology leads to more questions
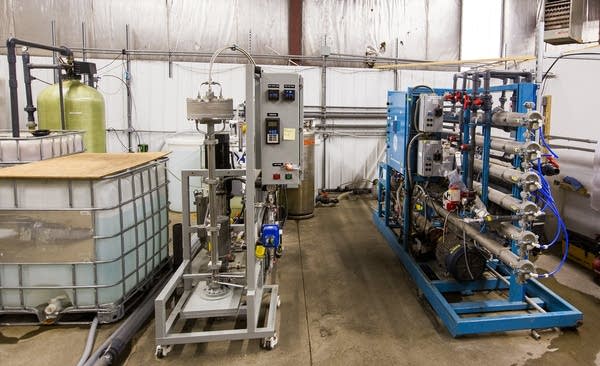
Go Deeper.
Create an account or log in to save stories.
Like this?
Thanks for liking this story! We have added it to a list of your favorite stories.
When it comes to the technologies mining companies employ to scrape minerals out of the ground, process them, and safely dispose of the waste, everything is on an immense scale.
One wheel on a truck is twice as tall as an adult. The plant where PolyMet Mining plans to process the ore it digs up is a third of a mile long.
The tailings basin near Hoyt Lakes, where PolyMet would slurry its leftover waste is massive, stretching to the horizon.
"If you look off in the distance, the skyline that you see out there, that's tailings all the way out to the ridgeline," PolyMet CEO Jon Cherry said recently, as he stood atop old iron ore tailings more than 20 stories high.
Turn Up Your Support
MPR News helps you turn down the noise and build shared understanding. Turn up your support for this public resource and keep trusted journalism accessible to all.
The area, which includes the old LTV Steel taconite plant that operated for about half a century, today looks like a vast grassland covering two square miles. It marks the spot where PolyMet plans to dispose of the waste from a huge copper mine in northeast Minnesota it plans to open nearby.
Minnesotans have until Thursday to comment on the environmental analysis of the proposed PolyMet mine, a huge document containing detailed plans on how the company would keep pollutants from the mine and tailings basin out of nearby lakes and rivers. That plan hinges on new technologies and engineering that PolyMet added after its last proposal was sharply criticized four years ago.
Along the north side of the vast tailings impoundment, the company plans to build a five mile long wall to capture water that runs through the tailings and picks up metals, sulfate and other pollutants. Company officials are confident the process will work.
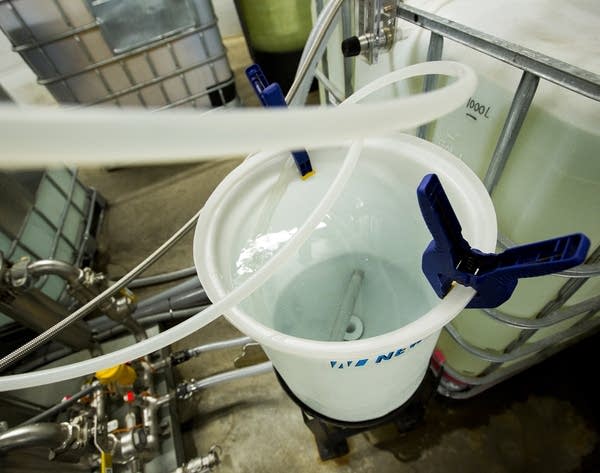
"The cut off wall that we're putting in, that will go all the way down to bedrock," Cherry said. "Those type[s] of technologies have been around for some time. This isn't like a new technology that we're trying out for the first time here."
Similar walls have proven successful at mines from Montana to Alaska, and at landfills around the country.
But few have been built as large, said Dave Chambers, president of the Center for Science and Public Participation in Montana.
"The concern with the slurry walls that are that big," he said, [is] "are you going to be able to guarantee that you're going to be able to anchor that slurry wall in bedrock along that whole perimeter?"
Chambers said the bedrock could fracture beneath the wall when it's installed, which could allow water to seep through.
The state's environmental impact statement predicts the cut-off walls will capture all surface water and 90 percent of groundwater that flows through the tailings. While the mine is operating, much of that water will be reused. After it closes, it will be treated using a process called reverse osmosis.
For two years the company operated a pilot water treatment plant to test the technology, tucked away in a small warehouse in the Iron Range town of Virginia, Minn.
Spokeswoman LaTisha Gietzen said the water is pretreated before it's pushed through the reverse osmosis filters, inside stacks of long white tubes.
"Under pressure, you squeeze the water through a membrane, the clean water comes out," she said.
LEARN MORE:PolyMet copper-nickel mining in Minnesota
PolyMet added reverse osmosis to its plans to help meet a strict state standard that limits the amount of sulfate that can be discharged into wild-rice producing waters.
The Navy first developed the technology to strip salt out of seawater. It's used in desalination plants around the world, but is still rare in mining. One place it has been used successfully is Utah, where two plants scrub groundwater that's been contaminated with a plume of sulfate created by a giant copper mine called Bingham Canyon that's operated for over a century.
Douglas Bacon, an environmental scientist for the Utah Department of Environmental Quality said the technology has worked extremely well since it came on line in 2006. It takes water with a sulfate concentration of 1,200 parts per million and reduces the concentration to below the state drinking water standard of 500 parts per million.
"But it comes at a cost," Bacon said.
•The PolyMet mining damage deposit: A landlord's advice
It costs the Utah facility $1.2 million dollars a year to treat 1.14 billion gallons of water.
"It has a hefty maintenance cost, because you've got to protect the membranes, which are subject to fouling and scale build up and abrasion, thus they can be broken down fairly quickly," Bacon said.
Maintenance costs at the PolyMet site are forecast to run between $3.5 and $6 million per year, which includes the cost of water treatment, according to the project's draft supplemental environmental impact statement.
"[The] DNR has described a mine that functions perfectly, exactly as intended, that has no problems whatsoever...but they don't explore scenarios in which something goes wrong."
Mines also have to dispose of the sludge leftover from the filtration process. At the Utah plant, that makes up about a quarter of the water that is fed into the system. PolyMet officials say the mine will recover a much higher percentage of the water, so sludge will only constitute about 5 percent, which will get hauled to a landfill offsite.
For the most part, PolyMet's skeptics are pleased the company added reverse osmosis. But some are still concerned there hasn't been enough consideration of what happens if something fails during the decades or even centuries the treatment plants may have to operate. DNR officials say emergency scenarios have been included in its analysis and would be more directly addressed in the permitting process, after the environmental impact statement is finalized.
But Kathryn Hoffman, an attorney for the Minnesota Center for Environmental Advocacy, said the environmental impact statement fails to analyze a scenario in which the process breaks down.
"[The] DNR has described a mine that functions perfectly, exactly as intended, that has no problems whatsoever," she said. "They do so, and they find it won't violate the Clean Water Act, and that it will meet all applicable laws, but they don't explore scenarios in which something goes wrong."
However, she said, past experience indicates that typically a problem arises.
"Usually it's not because the mine was poorly planned," she said. "It's because something went wrong."
Jess Richards, director of lands and minerals for the DNR, said the lead agencies did plan for unforeseen circumstances. But that's not always easy to see within the environmental impact statement, he said.
"There's scenarios embedded in the science, and also the assumption in some of the sections that some things could go wrong," he said. "There need to be some adaptive management techniques taken to correct it."
Richards said emergency planning also will be included in the mine's permitting, if it reaches that stage. But that won't start until the environmental impact statement is finalized and approved.
Editor's Note: An earlier version of this story was unclear about PolyMet's plans for the former LTV plant, which is where the company plans to dispose of the waste from its nearby copper mine. An earlier version also misstated the sulfate concentration in water before it is treated with reverse osmosis at a Utah facility. It is 1,200 parts per million, not 60,000 parts per million. The current version is correct.