New Minn. woolen mill finds unexpected markets
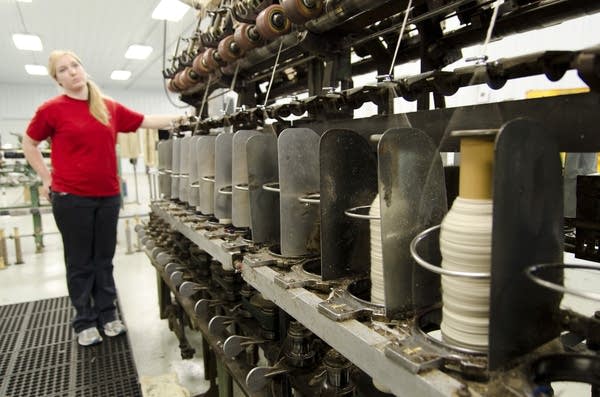
Go Deeper.
Create an account or log in to save stories.
Like this?
Thanks for liking this story! We have added it to a list of your favorite stories.
Inside a white metal building in a northern Minnesota industrial park, sit some of Stephanie Anderson's prized possessions: several old refurbished pieces of machinery that produce 100 pounds of yarn a day.
"This came out of Washington," Anderson said of one machine. "It was in storage for I don't know how many years. The spinning machine came from Spain. And then our plying machine came from a carpet mill in Georgia."
At capacity, eight to 10 people are needed to run Northern Woolen Mills, which largely produces wool. The company's machines also can spin other fibers and employees are working on 700 pounds of bison yarn for an east coast company that will use the yarn for socks.
A local market for sheep farmers
Turn Up Your Support
MPR News helps you turn down the noise and build shared understanding. Turn up your support for this public resource and keep trusted journalism accessible to all.
Founded last year, the mill is finding unexpected markets for its yarn, from the U.S. textile industry to Minnesota regional fiber artists excited to find a locally made product. It's also connecting with farmers in search of a market for spring wool.
Among them is Junior Farder, a northern Minnesota farmer who grows soybeans and wheat but who also has kept sheep for more than 50 years.
"It's a little extra income and they do a good job as far as cleaning up around the buildings," said Farder, 72. "They're good lawnmowers."
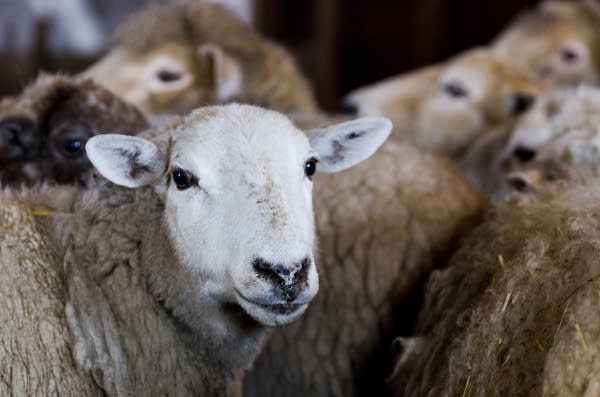
Spring shearing is a necessary chore. The heavy wool coat has to come off before lambs are born and the temperatures warm.
Most of the income earned from sheep comes from selling lambs in the fall. For years, Farder's wool went to a broker, and likely ended up at a mill in Asia.
Minnesota has about 135,000 sheep, 12th largest population in the nation, according to the U.S. Department of Agriculture. Their wool has often not been worth the cost of shearing, University of Minnesota extension agent Jim Stordahl said. For farmers like Farder, Anderson's mill helped change that.
"One of the exciting things about this woolen mill is that in the past there's been years when Junior would tell you he basically gave the wool away for the cost of shearing," Stordahl said.
This year Farder will haul the wool 17 miles down the road to Northern Woolen, which will pay him $1 a pound, or about $10, for each of his 47 fleeces.
The mill also received wool from as far away as Montana and Texas. Bison hair comes from North Dakota.
Workers at the mill also spin llama, camel, or dog hair brought in by customers. It takes three days from the time the wool or hair is washed until the yarn is spun and ready to use.
'A huge learning curve'
Anderson grew up in northern Minnesota and returned five years ago after spending much of her career in hotel management and marketing. She started the business last year after asking Bemidji Woolen Mills to make yarn.
The company's managers declined her request because they only make finished products. But they told Anderson people called every day with the same request.
"So I said 'Well, if you're getting calls every day and I know these yarn companies are looking for places to go, why isn't somebody doing it?'" Anderson recalled. "And they said, 'Nobody knows the textile industry anymore.' So I said, 'I'm sure I can figure it out.' And without giving it enough thought I just jumped in and did it."
If Anderson had taken the time to think about it, she might not have jumped into the textile business -- one she knew little about, and an industry that shut down hundreds of plants around the country since the late 1990s.
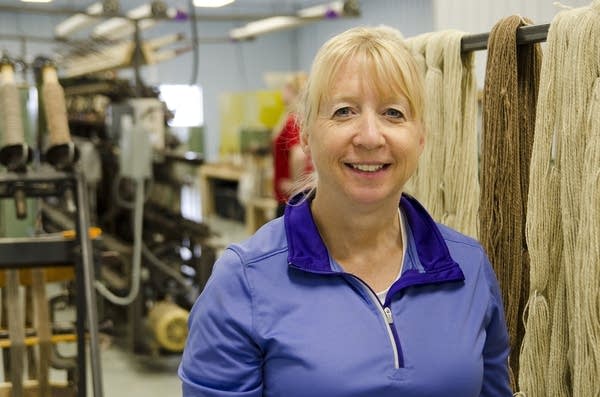
After receiving a $100,000 loan from the Fosston Economic Development Authority, and a price break from the city on land, Anderson mortgaged her home, invested her retirement fund and took the plunge.
"It has been a huge learning curve," she said. "I'm a knitter so I knew what I wanted at the end result, but I had no idea the process it went through to get it to the end."
The mill is proving a worthy competitor to mills in Asia, and Anderson expects to add a second shift soon, doubling the mill's production.
"I can't compete with the wages they pay their employees, but because of their added on shipping costs I can come pretty close, and I can hit their quality or better," Anderson said.