Fire and art: Forging strong ties at the U of M's iron pour
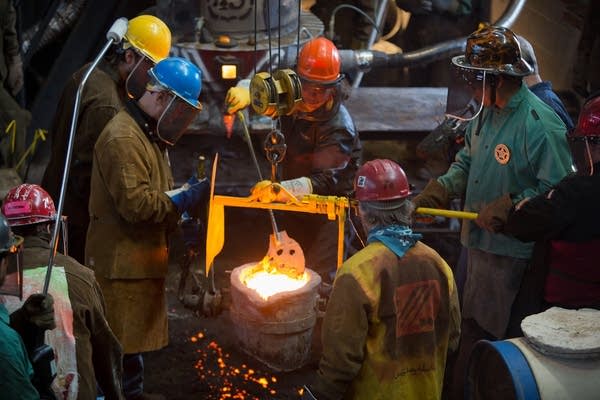
Go Deeper.
Create an account or log in to save stories.
Like this?
Thanks for liking this story! We have added it to a list of your favorite stories.
When you handle molten iron in a blazing furnace nearing 2,500 degrees, "you have to kind of know what you are doing."
Wayne Potratz made that point clear as he and his students Friday transformed liquid metal into art at the University of Minnesota's foundry. It was the art department's 45th Annual Iron Pour, an event that turns the foundry into a friendly, Hades kind of a place.
• Photo gallery: Pouring molten iron into art
The pour is always a special occasion. Glowing furnaces known as cupolas stand ready to melt metal. The artists, sculpture class students, come in all shapes and sizes: huge bearded men and diminutive, but equally tough looking, women. They all sport thick leather foundry clothes, hard hats and safety glasses. The place reeks of heated metal, a smell that weaves itself into everything.
Turn Up Your Support
MPR News helps you turn down the noise and build shared understanding. Turn up your support for this public resource and keep trusted journalism accessible to all.
This year, the crew is melting radiators scavenged by Potratz from the Northrop Auditorium remodeling project. The back of the stage "was all radiators and when they did that remodeling they took all those radiators out of there, and I got them," he said.
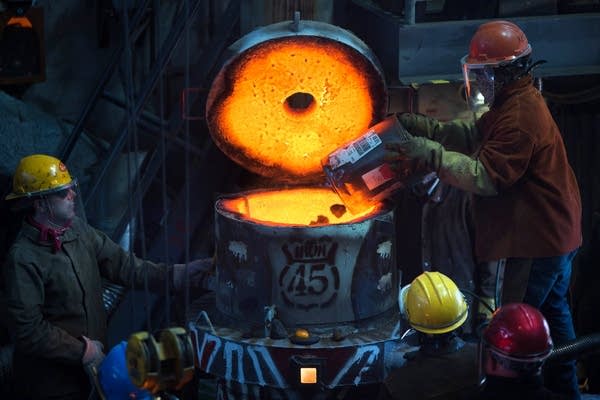
Outside the foundry three students break the radiators into pieces ready for melting. The pieces are taken inside the foundry and the warning horn blows to indicate the furnace is about to open, and the dance begins.
The furnace lid goes up and in goes five buckets of iron
The team calls out the number of buckets: "Four! Five!"
Twenty minutes later the 150 pounds of metal is molten and the dance continues. The same team carefully releases the stream of molten metal into bucket sized ladles and then pours the glowing liquid into the moulds. Immediately another team fills the furnace with the next load.
"It's a rush," student Sonia Johanson said afterward. "It's kind of like extreme sports for art, that's what I told my dad. It's definitely the most adrenaline when making a project I say, just the danger of it."
Potratz has traveled all over the world to other iron pours. He knows all about the metallurgy and the chemical reactions, but he also knows a huge amount about the lore too.
Photos: 45th annual Minnesota Iron Pour
"People who work with iron were always kind of shamanistic and shamans, especially in Africa," he said. "Recently I did a symposium in Ireland. They were talking about the Arthurian legend. And, when you think about it, probably what got Arthur his power was not that he could pull the sword out of the stone, but he could make the sword out of the stone."
Potratz joined the U in 1969. His predecessor had built a furnace, but Potratz hadn't used it. A student borrowed it to do an iron pour in Mankato. "And then he invited us down as a class and we poured iron and I was just bit by the bug," he recalled. "So I said give me my cupola back."
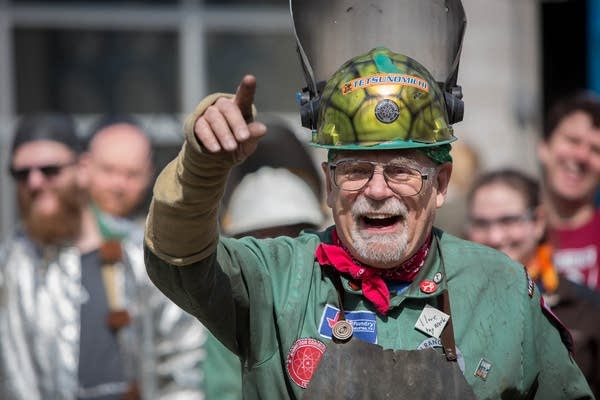
Potratz was particularly happy about the Northrop radiator haul.
He's retiring this year, but with the radiators he leaves behind a 10-year supply of iron for future pours. He did the department's first pour in 1970. Now he becomes a professor emeritus, and he'll no doubt continue to share his iron expertise.
"He talks wisdom," says U of M professor and sculptor Chris Larson who'll take over the foundry for the semester to keep it open as Potratz steps down.
He took Potratz's final class last year and said it was learning from a master.
It's not just about how the foundry works," Larson said. "It's about respect for materials and working through ideas and your process."
Larson says just teaching this class once has given him even more respect for Potratz.
"You have got to be so passionate to be in here to work with this level of intensity and hot metal," said Larson. "I don't know how he has done this for 45 years. I really don't. He must have a body of iron!"