Lean Health brings manufacturing efficiency to health care
Go Deeper.
Create an account or log in to save stories.
Like this?
Thanks for liking this story! We have added it to a list of your favorite stories.
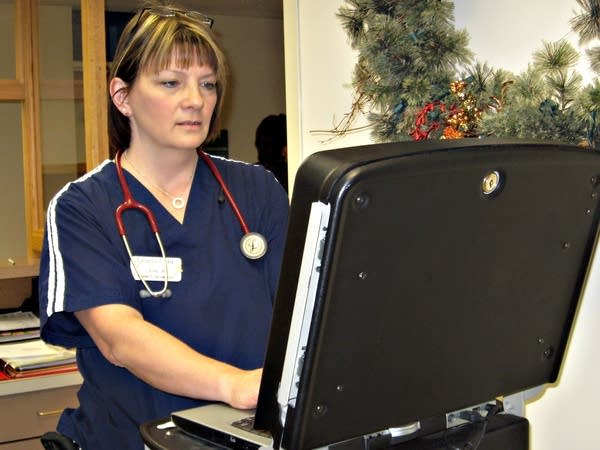
First Care Medical Services in Fosston, Minn., operates a relatively small hospital, with about 650 patients a year. But it's an important health care provider for the people in northwestern Minnesota, between Bemidji and Grand Forks.
"It's the one-two punch. Can we slow down the rising cost of health care and can we improve the quality through the reallocation of dollars saved?"
About four years ago this hospital was one of the first in the state to join the Lean Health Initiative.
The project's goal is saving money and improving patient care according to CEO Pat Wangler, not to shrink the 200-employee workforce.
"We don't believe we're overstaffed, but we believe we could use our staff better to produce a more satisfied patient, a safer environment and reduce errors," said Wangler.
Turn Up Your Support
MPR News helps you turn down the noise and build shared understanding. Turn up your support for this public resource and keep trusted journalism accessible to all.
A state grant to Northland Community and Technical College in Thief River Falls set up classes that allowed hospital staff to learn the principles of lean health.
Pat Wangler said things started changing soon after employees were asked to look at their jobs differently.
"What they're doing is looking at the processes they do that when they come to work they say 'Oh, I knew that would happen', or 'Oh, it happened again,'" Wangler explained.
Some of the changes have been small; like giving housekeeping staff screwdrivers so they don't have to put in a work order if they find a loose screw on a light switch.
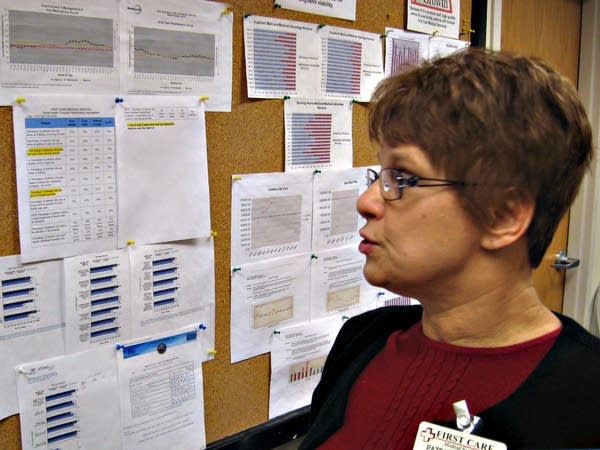
Other efficiencies have greater impact. Changing to electronic billing resulted in an annual savings of 1,500 hours that had been spent filing and shuffling paper. That saved thousands of dollars and it means the small billing department staff can now spend more time working with patients to set up payment plans and follow up on unpaid bills.
Employees also developed more efficient tracking methods for supplies and medication which means less money is tied up in excess inventory sitting on shelves.
"We measure it by time saved that is then put into another process we couldn't do before," said Wangler. "We measure it in outcomes and we believe we've really achieved improved outcomes and improved satisfaction."
A major lean health project now underway at First Care aims to have nurses spend at least 70 percent of their time with patients.
"I have my entire nurse's desk with me whenever I have my computer. Everything I need to know is in the computer with me," explains Laura Woolliscroft. R.N., as she types on a laptop that sits on a wheeled cart.
Nurses jokingly refer to the computers as COWS, short for computer on wheels. But the efficiency the computer creates is no joke.
Woolliscroft said time spent sitting at the nurses station doing paper work was one of the biggest frustrations for nurses. So nurses now take the COW everywhere with them.
Any change in a patient's record is made at the bedside. Woolliscroft said that makes her more efficient, but it also reduces the potential for mistakes. If a doctor orders a medication stopped, the change is made immediately, not an hour later when the nurse has a chance to catch up on paperwork.
Nurses on duty also carry phones so they don't need to return to the nurse's station to take calls.
"When I spend the majority of my time at the nurse's desk I don't feel like I've served the patients as well as I should as a registered nurse," said Woolliscroft. "I feel like I've done more of the clerical work which is not the career I chose when I went into nursing. The more time I spend with patients, the happier nurse I am when I go home at night."
It appears patients are happier too, according to surveys that track patient satisfaction at First Care.
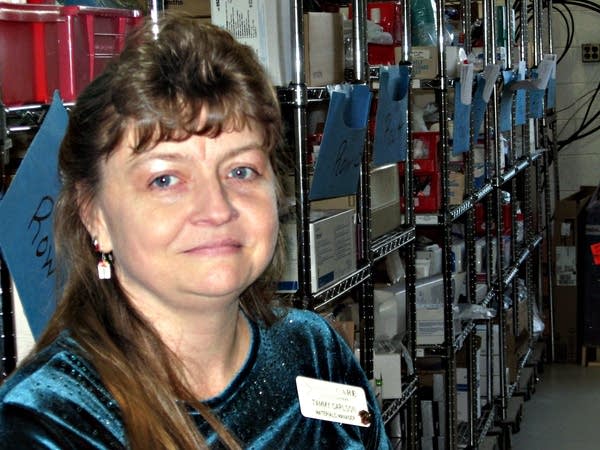
Some of those satisfied patients might be employed at regional companies that helped develop the Lean Health Initiative.
Digi-Key Vice President for Human Resources Rick Trontvet, represents the Thief River Falls-based electronics supplier on the lean health steering committee.
Access to high quality health care is critical to retaining employees, according to Trontvet. Health insurance costs are an increasing burden on the company and its employees.
"We think this is one pretty cool strategy that can actually benefit everybody because if the costs are held at bay a little bit everybody can benefit," said Trontvet. "It's the one-two punch. Can we slow down the rising cost of health care and can we improve the quality through the reallocation of dollars saved?"
The first Lean Health Initiative grant from the state Department of Employment and Economic Development was awarded in 2004. Since then DEED has awarded 15 grants that trained 4,700 workers at 30 Minnesota hospitals and clinics.
DEED Commissioner Dan McElroy said the state has spent $3.7 million on lean health, and medical facilities have contributed $8.3 million to the process.
"The track record is we get three things from that," said McElroy. "People stay and advance in their careers so they make more money, we add wealth to communities. The quality of health care and patient satisfaction increases. And the long term costs either don't go up as much because they're more efficient, there are fewer steps done."
The Lean Health Initiative that started in northwest Minnesota four years ago has not gotten much attention according to McElroy, but the idea is slowly spreading across the state.
He called it a grassroots movement which he expects to become an essential tool for any medical facility that wants to remain competitive in the future.