QBP sketches plans for a Minnesota-made bike
Go Deeper.
Create an account or log in to save stories.
Like this?
Thanks for liking this story! We have added it to a list of your favorite stories.
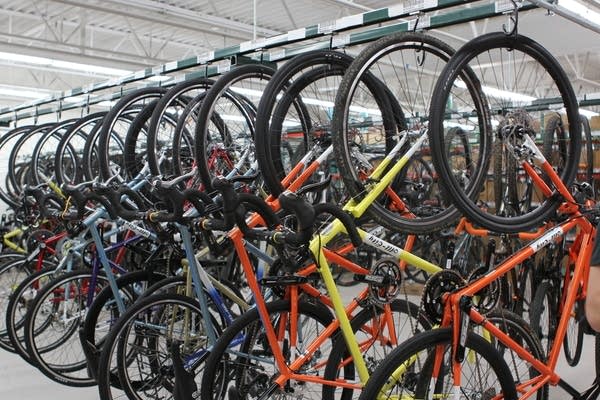
Minnesota boutique bike makers have been building for years on a small scale and charging a hefty price. One local parts maker and distributor, though, has plans to get bigger, make money and ship globally while still keeping his bike building operation home-grown.
“We believe that we can start manufacturing bikes right here in Minnesota. That’s in our game plan,” said Steve Flagg, chief executive of Bloomington-based Quality Bicycle Products.
It's a risky idea, no doubt. Roughly 95 percent of bikes sold in the world are produced in Taiwan or China and production costs are a big question.
Still, bike builders have long called Minnesota home and Flagg has a history of success.
Turn Up Your Support
MPR News helps you turn down the noise and build shared understanding. Turn up your support for this public resource and keep trusted journalism accessible to all.
A University of Minnesota economics grad, he started QBP in 1981 in a small office in St. Paul supplying bike parts to local shops. In 2010, the university named Flagg its entrepreneur of the year.
The company now distributes parts to more than 5,000 independent bike dealers and serves commuters and other bikers under numerous brands.
Making bikes here is a big leap but feels like a return to the type of risk the company took early on, Flagg said. “We’re already building 70,000 wheels in Minnesota, doing bike assembly. It’s not out of reach for us. "
QBP is set up as a distributor. "To do the welding and painting we’ll need a separate but nearby facility,” Flagg explained. “We’ll begin that hunt pretty soon.” He hopes to start producing bikes within two years.
While Minnesota is home to many of the raw materials needed in the bike building process, the manufacturing support for key parts will likely have to come from Asia.
“We’ll source out tubing [for the bike frame], and then we’ll cut, miter, weld and then do assembly at our existing facility,” Flagg says. “We do a lot of it already. I don’t think it’s that much of a stretch for us. I think we’re closer than we think.”
With reporting from Molly Bloom