School of Rock: Red Wing guitar builders hit the right notes
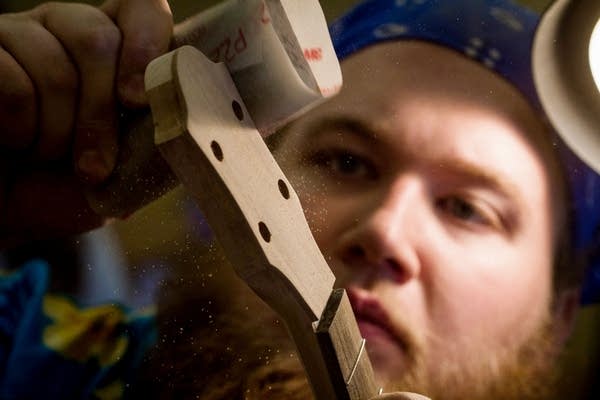
Go Deeper.
Create an account or log in to save stories.
Like this?
Thanks for liking this story! We have added it to a list of your favorite stories.
For 19-year-old Eli Napolski, removing all the tiny scratches from his first hand-built guitar is a labor of love — and patience. He's been sanding for two days.
Hunched over his work bench, he teases out the scratches with a sanding block. He's played guitar for six years but until August, the White Bear Lake native didn't know much about how to make the instrument. A few minutes more sanding and he holds up the unstained, unfinished acoustic guitar for inspection.
"This is spruce, mahogany for the back and sides," he says, showing off the piece to a visitor. "The fingerboard is ziricote, which looks awesome. And then walnut. This is looking to be a pretty nice guitar."
Napolski's among a few dozen students in this year's guitar repair and building program at Southeast Technical — a Minnesota State College in Red Wing.
Turn Up Your Support
MPR News helps you turn down the noise and build shared understanding. Turn up your support for this public resource and keep trusted journalism accessible to all.
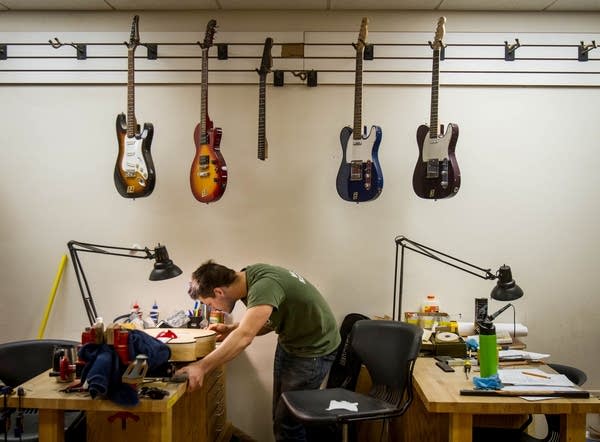
While other college students are writing papers or taking exams as spring semester ends, Napolski and his classmates are sanding, spraying and fine-tuning nearly 80 hand-crafted instruments. They'll be put to the test Tuesday when Twin Cities musicians play them as part of the school's annual student guitar show.
Southeast Tech boasts that it runs the country's most robust, multi-year guitar building program. In some schools, instruction runs only a month or two and doesn't teach guitar repair. Others teach guitar assembly but not necessarily how to work the wood.
Here, students go from raw wood to a fully finished guitar in the first year. In the second, students learn computer numerical control machines and computer-aided design, as well as more intricate, advanced finishes, too.
"People usually come here because they're interested in guitars," said instructor Steve Rossow. "We get people who are right out of high school who have an interest in guitars and we also get a lot of retired people who have had this interest in them their whole lives and now they have time to come back and pursue that."
Although it's not an associate's degree, first-year students come away with a guitar repair and building diploma. Second-year students earn a separate guitar development and production diploma.
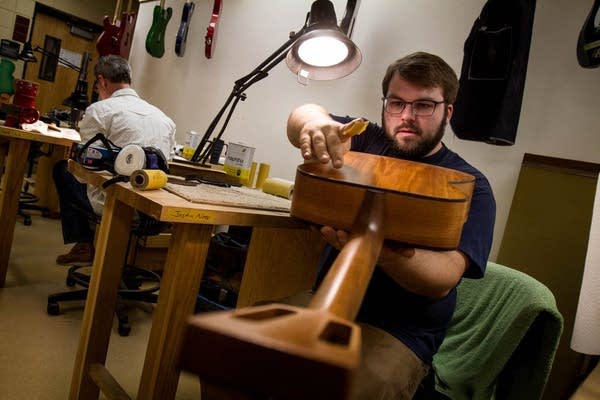
By year two, some also build mandolins, ukuleles and hurdy gurdys, which looks like a guitar with a wooden box and a basic keyboard sitting where the strings are. The tone comes when a wheel rubs against the strings. It lets people who don't know guitar fingerings play a tune using single or multiple strings.
Many of the students are musicians, but a lot of them don't have any woodworking experience. They learn to transform raw slabs of lumber into musically sound instruments.
"We assume the students coming in have no experience with really any hand tools, power tools, woodworking skills at all, so we start from the very, very beginning," Rossow said.
The painstaking work isn't always easy. Rossow says there's one part of the process that stumps students all the time.
"Fitting necks to the bodies seems to be one of those challenging parts," he said. "You're trying to fit one, two, three, four, five surfaces to five different surfaces and you're trying to get the angle of the neck, the center line, the twist, all of this stuff has to line up just right..."
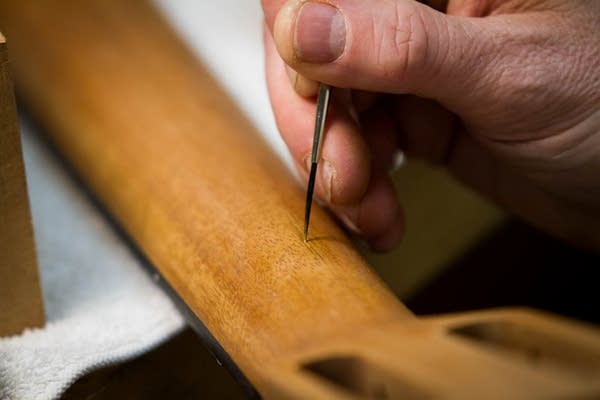
Lining parts up just right is particularly challenging this year for 27-year-old Michael Opp of Jamestown, N.D. Opp has a bachelor's degree in music, but decided building instruments was a better way to earn a living.
Opp twists a drill bit to remove lacquer from the tuning peg holes.
"I'm going to try to find a job building hurdy gurdys and if not, start my own business building hurdy gurdys," he said. ""his is what I want to do with the rest of my life."
Making that career a reality can be tough. Rossow says it can take years for students to successfully sell their instruments on their own. Six of 18 graduates from 2012 are working either full or part-time jobs in a related field, according to the college's most recently available job placement data.
Duluth native Currin Effinger is one student this year with a few job prospects already lined up. The 19-year-old plans to work for Myka Guitars, a company that builds hand-crafted instruments out of Seattle.
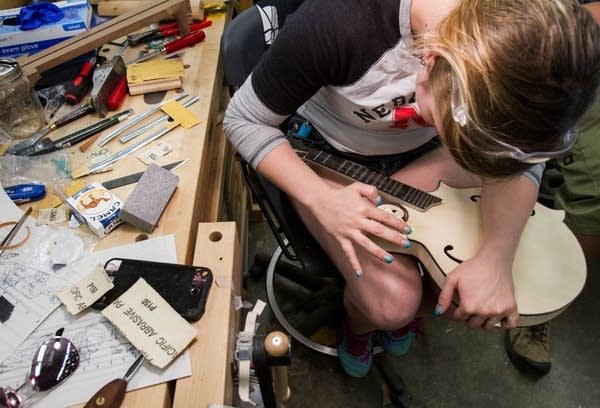
He's already finished his final exam — a 17-inch cranberry red archtop guitar that will be ready for its debut on Tuesday.
The payoff for all the hard work, he notes, goes way beyond a diploma: "To be able to play your own instrument once you're done and fiddle around on it and know that I built this with my own hands, I made the guitar sound how it sounds ... it's amazing."
If you go: Southeast Technical Student Guitar Show
When: Tuesday, 11 a.m. to 1 p.m.
Where: Minnesota State College - Southeast Technical, 308 Pioneer Rd., Red Wing
Notable: The event includes concerts on two stages and a display of new musical instruments. Admission is free.