Fargo scientists search for next generation of plant-based plastics
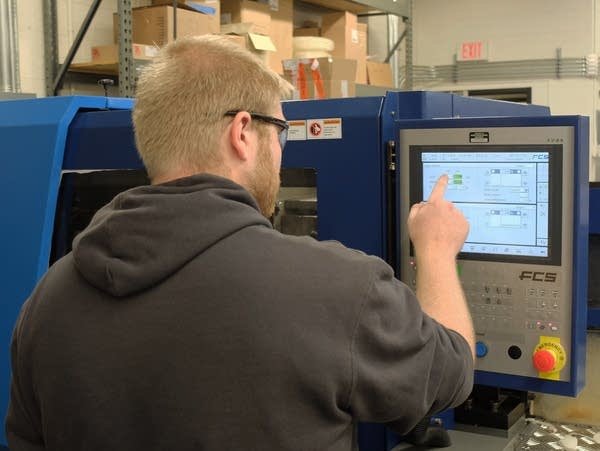
Go Deeper.
Create an account or log in to save stories.
Like this?
Thanks for liking this story! We have added it to a list of your favorite stories.
In a noisy industrial lab at North Dakota State University, graduate students make dog bones with an injection molding machine — but there are no dogs in sight. The students are researchers, and they use the bone-shaped plastic pieces to test the strength of new bioplastics — plastics made out of plant material, like wheat germ, corn, soybeans and plant-based polymers.
This research effort — formally, the Center for Bioplastics and Biocomposites — is based at NDSU but happening in conjunction with three other universities: Iowa State, the University of Georgia and the University of Washington.
And while bioplastics have only a tiny share of the plastics market today, some major companies — the Ford Motor Company, The Coca-Cola Company and 3M — are joining the research effort. Scientists expect more plant-based plastics to find their way into everyday products.
NDSU professor David Grewell oversees the entire project. Bioplastics, he said, make up less than three percent of the plastics market, but that’s changing.
Turn Up Your Support
MPR News helps you turn down the noise and build shared understanding. Turn up your support for this public resource and keep trusted journalism accessible to all.
“If we look at, for example, what Coca-Cola does, many of their bottles are up to one-third bio-based, and so that is a good example of where the bio-economy is growing,” Grewell said. “We see about a 15 to 20 percent growth of the bioplastics industry — and if my 401(k) was growing at 15 to 20 percent a year, I'd be very happy.”
Car companies are using bioplastics in new vehicles, and more food packaging is often bio-based plastic, too.
But it can be difficult for consumers to know when they are using a product made out of bioplastic. Sometimes those items are identified, but Grewell said the industry doesn’t employ standard labeling — like the numbers in the upside-down triangles that are used to show consumers which plastics can be recycled. If they are labeled, bioplastics will often be assigned a #7, a catchall label for “other plastics.”
The goal of the research initiative is to replace some of the petroleum-based plastics that dominate the market with plant-based material — in everything from beverage bottles to car parts, because bioplastics, contrary to what some might think, are not necessarily biodegradable.
“Ford Motor Company would not want to put a component in a vehicle that is going to break down in a couple years,” Grewell said. “These things need to last for a long time, so we need to do a little bit better job of educating the public.”
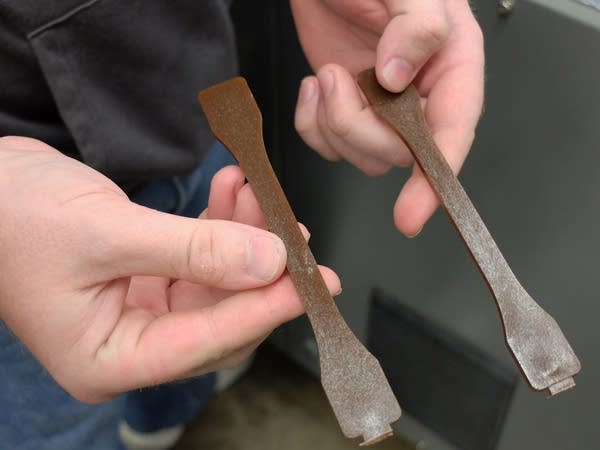
Some bioplastics can be composted, but not in a backyard compost pile. They require an industrial composting process with extreme heat. And that flexibility is offering researchers a host of different questions to consider.
“One I think of is, ‘How long does the product really need to last?’” said NDSU professor Dean Webster.
Webster, who is the Fargo site director for the research initiative, has been developing petroleum-based polymers — materials that stick together — for more than three decades. Now he’s working to develop plant-based alternatives. And while there’s a century of science behind petroleum-based materials, he said, plants offer scientists a whole new range of chemical and physical properties.
“You know, we have these plastic products that last forever,” he said. “Well, do we use them forever? And what really is their lifetime? We're asking those questions now, which I think is a really good thing.”
Webster is working to create plant-based material that could be used in 3-D printing, something that is long-lasting, but could also be recycled using a specific chemical process. He said such a material would be useful to companies developing new products, which often print dozens of prototypes — producing lots of waste — before they finalize a design.
“Well, now you have a whole bucket of stuff you're going to throw away,” he said. “So if there was an opportunity to degrade those and then reuse that — recycle it into more printing material — that would be awesome.”
As they develop plant-based plastics, Grewell said, researchers have stumbled across some unexpected benefits, because plants have some chemical properties that are hard to create in a lab.
For example, one type of small pot that’s used for starting greenhouse plants — is made from soy and corn. It breaks down in the soil. But researchers were surprised to find that these pots did not create a problem common to potted plants: The roots did not grow in a circle inside the pot. So when it came time to plant the seedlings in the ground, the plants were healthier, with looser roots.
Grewell said he anticipates finding more unexpected benefits as he and his colleagues spend more time analyzing plant-based materials.
Danny Mishek’s company, SelfEco, manufactures those bioplastic plant-starter pots, as well as bioplastic food service items like champagne flutes.
“There's a huge opportunity to grow into that market share,” he said. “We’re kind of changing the paradigm, and so there’s not a lot of research out there to help us.”
Mishek said he thinks the bioplastics industry is confusing to most consumers, who don’t understand what bioplastics are and how they can be more sustainable than plastics made from petroleum, because they use parts of plants already in production.
“We're not using the corn kernels. We're using the corn roots and the corn stock,” he said. “So that corn’s going to be grown anyways for feedstock.”
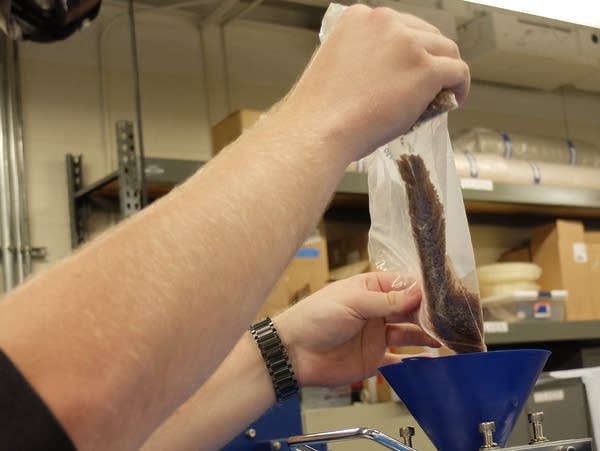
The products made from bioplastics are often more expensive than those made from petroleum-based plastics, and some environmentalists argue that growing plants for plastic leads to land use that’s not good for the environment, and increases water use. But Mishek argues it’s better than the alternative, especially for plastic products used for only a short time.
“If you're going to take corn stocks or corn roots from a feedstock that’s already being grown, that beats drilling into the planet for oil,” Mishek said. “There’s not a silver bullet here. It’s not ‘This is the total solution.’ It’s part of the solution.”
The Center for Bioplastics and Biocomposites is funded by the National Science Foundation, with help from several major U.S. companies, which also help researchers decide which projects move forward.
Grewell said the goal, in the partnership, is to create sustainable materials that are useful and affordable.
“Does it make sense to do this from the environmental point of view?” he said. “Does it make sense to do this from an economical standpoint? If I can't do this and still make money then I can't do this.”
Grewell said he thinks that as more companies try to prove to consumers they are sustainable, plant-based products have a bright future, whether they’re made of corn stalks, wheat straw or hemp fibers.