How are ancient Roman and Mayan buildings still standing? Scientists are unlocking their secrets
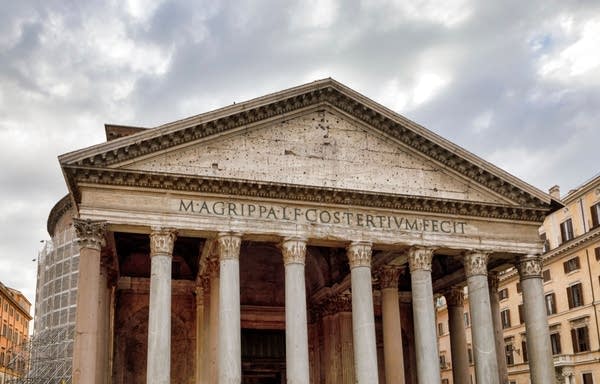
Go Deeper.
Create an account or log in to save stories.
Like this?
Thanks for liking this story! We have added it to a list of your favorite stories.
In the quest to build better for the future, some are looking for answers in the long-ago past.
Ancient builders across the world created structures that are still standing today, thousands of years later — from Roman engineers who poured thick concrete sea barriers, to Maya masons who crafted plaster sculptures to their gods, to Chinese builders who raised walls against invaders.
Yet scores of more recent structures are already staring down their expiration dates: The concrete that makes up much of our modern world has a lifespan of around 50 to 100 years.
A growing number of scientists have been studying materials from long-ago eras — chipping off chunks of buildings, poring over historical texts, mixing up copycat recipes — hoping to uncover how they’ve held up for millennia.
Turn Up Your Support
MPR News helps you turn down the noise and build shared understanding. Turn up your support for this public resource and keep trusted journalism accessible to all.
This reverse engineering has turned up a surprising list of ingredients that were mixed into old buildings — materials such as tree bark, volcanic ash, rice, beer and even urine. These unexpected add-ins could be key some pretty impressive properties, like the ability to get stronger over time and “heal” cracks when they form.
Figuring out how to copy those features could have real impacts today: While our modern concrete has the strength to hold up massive skyscrapers and heavy infrastructure, it can't compete with the endurance of these ancient materials.
And with the rising threats of climate change, there's a growing call to make construction more sustainable. A recent UN report estimates that the built environment is responsible for more than a third of global CO2 emissions — and cement production alone makes up more than 7% of those emissions.
“If you improve the properties of the material by using … traditional recipes from Maya people or the ancient Chinese, you can produce material that can be used in modern construction in a much more sustainable way,” said Carlos Rodriguez-Navarro, a cultural heritage researcher at Spain’s University of Granada.
Is ancient Roman concrete better than today's?
Many researchers have turned to the Romans for inspiration. Starting around 200 BCE, the architects of the Roman Empire were building impressive concrete structures that have stood the test of time — from the soaring dome of the Pantheon to the sturdy aqueducts that still carry water today.
Even in harbors, where seawater has been battering structures for ages, you’ll find concrete “basically the way it was when it was poured 2,000 years ago,” said John Oleson, an archaeologist at the University of Victoria in Canada.
Most modern concrete starts with Portland cement, a powder made by heating limestone and clay to super-high temperatures and grinding them up. That cement is mixed with water to create a chemically reactive paste. Then, chunks of material like rock and gravel are added, and the cement paste binds them into a concrete mass.
According to records from ancient architects like Vitruvius, the Roman process was similar. The ancient builders mixed materials like burnt limestone and volcanic sand with water and gravel, creating chemical reactions to bind everything together.
Now, scientists think they’ve found a key reason why some Roman concrete has held up structures for thousands of years: The ancient material has an unusual power to repair itself. Exactly how is not yet clear, but scientists are starting to find clues.
In a study published earlier this year, Admir Masic, a civil and environmental engineer at the Massachusetts Institute of Technology, proposed that this power comes from chunks of lime that are studded throughout the Roman material instead of being mixed in evenly. Researchers used to think these chunks were a sign that the Romans weren’t mixing up their materials well enough.
Instead, after analyzing concrete samples from Privernum — an ancient city outside of Rome — the scientists found that the chunks could fuel the material’s “self-healing” abilities. When cracks form, water is able to seep into the concrete, Masic explained. That water activates the leftover pockets of lime, sparking up new chemical reactions that can fill in the damaged sections.
Marie Jackson, a geologist at the University of Utah, has a different take. Her research has found that the key could be in the specific volcanic materials used by the Romans.
The builders would gather volcanic rocks left behind after eruptions to mix into their concrete. This naturally reactive material changes over time as it interacts with the elements, Jackson said, allowing it to seal cracks that develop.
The ability to keep adapting over time “is truly the genius of the material,” Jackson said. “The concrete was so well designed that it sustains itself.”
Using tree juice to make sculptures as strong as seashells
At Copan, a Maya site in Honduras, intricate lime sculptures and temples remain intact even after more than 1,000 years exposed to a hot, humid environment. And according to a study published earlier this year, the secret to these structures' longevity might lie in the trees that sprout among them.
Researchers here had a living link to the structures' creators: They met with local masons in Honduras who traced their lineage all the way back to the Mayan builders, explained Rodriguez-Navarro, who worked on the study.
The masons suggested using extracts from local chukum and jiote trees in the lime mix. When researchers tested out the recipe — collecting bark, putting the chunks in water and adding the resulting tree “juice” into the material — they found the resulting plaster was especially durable against physical and chemical damage.
When scientists zoomed in, they saw that bits of organic material from the tree juice got incorporated into the plaster’s molecular structure. In this way, the Mayan plaster was able to mimic sturdy natural structures like seashells and sea urchin spines — and borrow some of their toughness, Rodriguez-Navarro said.
Studies have found all kinds of natural materials mixed into structures from long ago: fruit extracts, milk, cheese curd, beer, even dung and urine. The mortar that holds together some of China’s most famous structures — including the Great Wall and the Forbidden City — includes traces of starch from sticky rice.
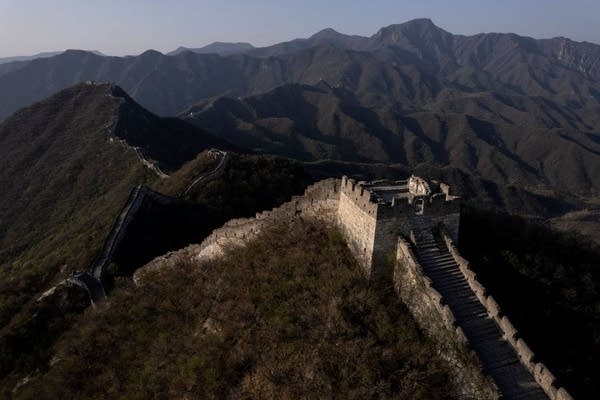
Luck or skill?
Some of these ancient builders might have just gotten lucky, said Cecilia Pesce, a materials scientist at the University of Sheffield in England. They’d toss just about anything into their mixes, as long as it was cheap and available — and the ones that didn’t work out have long since collapsed.
“They would put all sorts of things in construction,” Pesce said. “And now, we only have the buildings that survived. So it’s like a natural selection process.”
But some materials seem to show more intention — like in India, where builders crafted blends of local materials to produce different properties, said Thirumalini Selvaraj, a civil engineer and professor at India’s Vellore Institute of Technology.
According to Selvaraj’s research, in humid areas of India, builders used local herbs that help structures deal with moisture. Along the coast, they added jaggery, an unrefined sugar, which can help protect from salt damage. And in areas with higher earthquake risks, they used super-light “floating bricks” made with rice husks.
“They know the region, they know the soil condition, they know the climate,” Selvaraj said. “So they engineer a material according to this.”
Ancient Roman ... skyscrapers?
Today’s builders can’t just copy the ancient recipes. Even though Roman concrete lasted a long time, it couldn't hold up heavy loads: “You couldn’t build a modern skyscraper with Roman concrete,” Oleson said. “It would collapse when you got to the third story.”
Instead, researchers are trying to take some of the ancient material’s specialties and add them into modern mixes. Masic is part of a startup that is trying to build new projects using Roman-inspired, “self-healing” concrete. And Jackson is working with the Army Corps of Engineers to design concrete structures that can hold up well in seawater — like the ones in Roman ports — to help protect coastlines from sea level rise.
We don’t need to make things last quite as long as the Romans did to have an impact, Masic said. If we add 50 or 100 years to concrete’s lifespan, “we will require less demolition, less maintenance and less material in the long run.”