Consultant suggested monitors for critical parts of I-35W bridge
Go Deeper.
Create an account or log in to save stories.
Like this?
Thanks for liking this story! We have added it to a list of your favorite stories.
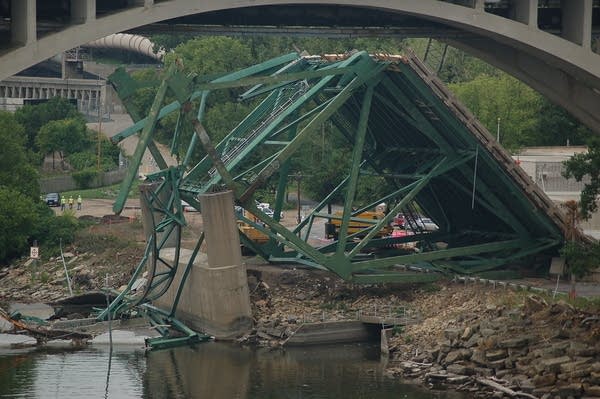
(AP) - A consultant for the state Transportation Department recommended installing high-tech sensors to detect cracking on critical sections of the Interstate 35W bridge less than a year before the bridge collapsed, according to documents obtained by The Associated Press.
The recommendation made in the November 2006 report was rejected, but one expert in the sound-based monitoring technology said even the suggestion that so-called "fracture critical" sections of the bridge were susceptible for cracking should have sent up a warning flare.
"For somebody to be looking for cracks to initiate in a fracture critical member begs the question, why?" said John Duke, a professor of engineering science and mechanics at Virginia Tech who's researched acoustic emission monitoring.
The bridge collapsed on Aug. 1, killing 13 people and injuring about 100. The AP reviewed nearly 13,000 pages of documents obtained under a Data Practices request relating to a contract MnDOT had with URS Corp. to investigate the safety of the aging bridge.
Learn how to have civil, political conversations with our e-book Talking Sense
Political debates with family or friends can get heated. But what if there was a way to handle them better?
Download our free e-book, "Talking Sense: Have Hard Political Conversations, Better," and learn how to talk without the tension.
"When a fracture critical member is discovered to have a crack, that bridge should have been shut down yesterday."
Duke said if a fracture critical component on a bridge fails, that means the entire bridge fails. A crack in one of those pieces would be extremely dire, and he questioned if an acoustic emission monitor would have been able to pick it up in time.
"When a fracture critical member is discovered to have a crack, that bridge should have been shut down yesterday," he said.
In the years leading up to the collapse, MnDOT itself and private consultants performed numerous evaluations and inspections of the bridge that raised concerns about its condition.
It contracted with URS in 2003 to perform a more thorough analysis of fatigue in the bridge support structure. Presented with options for addressing safety concerns, MnDOT chose increased inspections rather than more expensive repairs.
Dan Dorgan, MnDOT's state bridge engineer, said the acoustic monitors were considered, but the agency ultimately went with other kinds of inspections because there were no signs of fatigue cracking on bridge trusses.
"In the absence of cracks, we had no locations to monitor or information to orient monitors for crack detection," Dorgan wrote in response to written questions from the AP.
Still, URS Corp. indicated in its study of the bridge between 2004 and 2006 that there were 20 fracture critical truss beams on the bridge - those considered after inspection to be "the most susceptible locations for crack initiations."
While the URS study indicated that "no cracks are believed to be in existence currently," a monitoring system would "timely report any signs of crack initiation and/or propagation."
Dorgan said that MnDOT inspectors instead utilized ultrasonic testing, which he called a "proven means of actually detecting cracks."
Ron Low, a spokesman for URS, said that the company would not comment on any of the findings or recommendations related to its inspections of the bridge.
Mark Carlos, president of a company that makes such monitors, said there's no way to know if such monitors would have detected an impending bridge failure collapse. But, he said, if monitors had been placed in the right spots, they might have sensed if the bridge was reaching "a critical state in cracking."
"As it gets more and more intense, the cracking becomes more critical and you start detecting more cracking events more quickly," Carlos said.
Carlos' firm, Physical Acoustics Corporation, was among those that a URS official mentioned in one e-mail as a possible contractor to provide crack monitors, but Carlos said the company never did any work for MnDOT.
The URS study recommended that the acoustic emission monitoring system include the capability of alerting MnDOT immediately regarding specific locations on the bridge "where unusual signals are detected indicating the possibility of steel cracking."
The system recommended by URS included a backup solar-powered generator so the bridge would have "non-interrupted monitoring" if there was a short-term power outage, the study said.
Carlos said acoustic emission monitoring differs from the way bridges are typically inspected; it detects cracks while they are occurring, instead of trying to spot them after they've happened.
He said the cost of installing the monitors in a specific area of a bridge, as was proposed by URS, would cost between $20,000 to $40,000. He said the devices are used on some bridges around the country but are not yet common.
As part of the plans for the 35W replacement bridge, designers have proposed a sensor and monitoring system that will be installed to create what they call a "smart bridge."
First, sensors will be used as the bridge is built to determine the maturity of the concrete, said Linda Figg, who heads Figg Bridge Engineers Inc. of Tallahassee, Fla., the lead design firm on the team picked to replace the fallen bridge.
"Then once the bridge is built, sensors will provide data on a long-term basis to provide information about the structure," Figg said. "It's using state-of-the-art technology to create a bridge for the future."
Details on the sensor system still need to be worked out with MnDOT, but designers said the goal is to arm transportation officials with real-time data on everything from structural bridge responses to deck moisture to wind speed.
(Copyright 2007 by The Associated Press. All Rights Reserved.)