Six months after collapse, 35W bridge rebuild is ahead of schedule
Go Deeper.
Create an account or log in to save stories.
Like this?
Thanks for liking this story! We have added it to a list of your favorite stories.
There are more than 200 construction workers at the site next to the Mississippi River in Minneapolis where the old bridge collapsed and where the new one is being built.
The first plan was to cast the individual concrete bridge segments down-river and use barges to haul them to the site. That changed when engineers realized there's room on the currently closed freeway roadbed next to the river for the casting sheds.
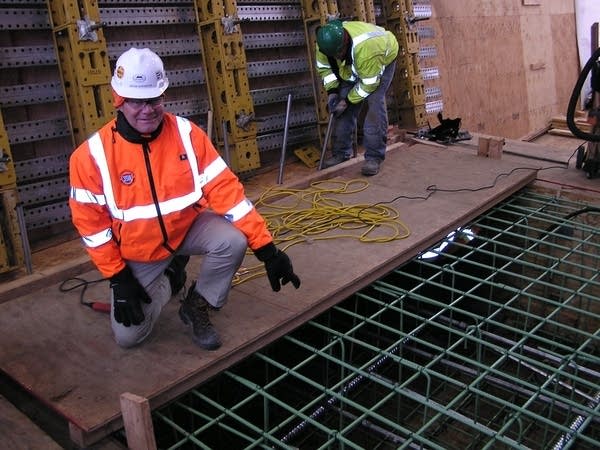
The four-story-tall metal casting sheds are where workers are building the plywood and reinforcing steel bar forms for the bridge segments. Outside the air temperature is barely above zero. Inside the sheds it's well above freezing with the aid of warm air pumped in by portable heaters thrumming in the background.
Concrete is a major component of the new bridge. More will be poured for the new span than was used to build the nearby Metrodome.
Turn Up Your Support
MPR News helps you turn down the noise and build shared understanding. Turn up your support for this public resource and keep trusted journalism accessible to all.
Engineer Peter Sanderson says concrete needs temperatures above freezing to cure properly. Along with temperature the concrete recipe, Sanderson says, has to be just right.
"The first five trucks we had to reject. They were too low in air content," he says.
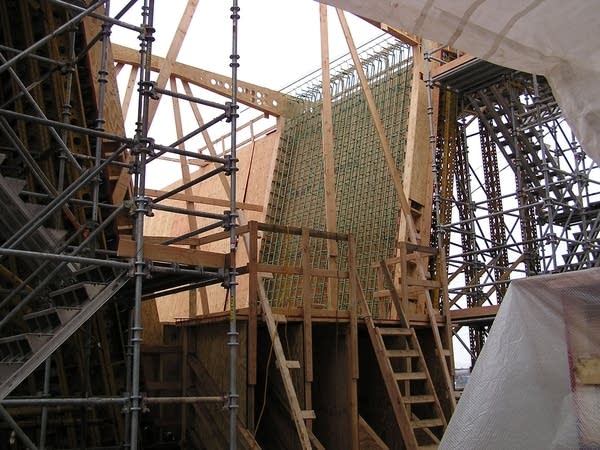
The air entrainment, Sanderson calls it, wards off damage to concrete from freeze and thaw cycles - a problem here in Minnesota where annual temperatures vary widely.
"There are little tiny bubbles of air throughout the concrete that help insulate the concrete itself, it certainly gives you more durable concrete," he says.
Along with concrete the other major building material in the bridge is steel - 17 million pounds of green coated steel reinforcing rods. The concrete is poured around the rods inside the plywood form. The rods create a three dimensional maze. Together the concrete and steel form the strength of the bridge. There's nothing haphazard about the bending and placing of the steel rods or rebar in the individual bridge segments, Sanderson says.
"There's an exact spacing, size spacing, both ways of each particular size bar we're looking at. This is what carries the load, this is what will be carrying the new freeway," Sanderson says.
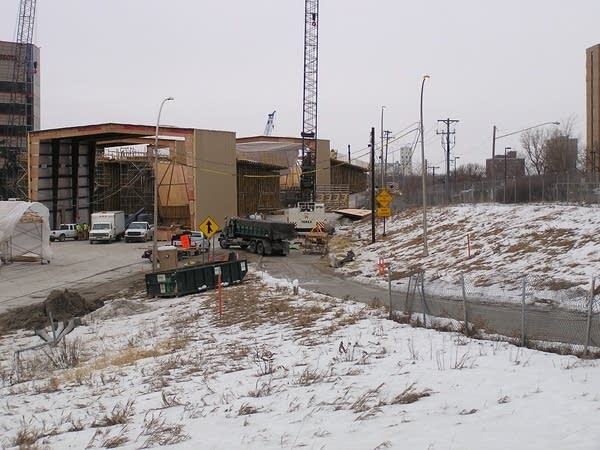
The concrete recipe includes chemical additives to retard the corrosion of the steel rods, Sanderson says. Lots of salt is used on Minnesota's roads and bridges to melt ice and snow. That's good for safety, but bad for bridges as the salt seeps into concrete and corrodes the steel inside.
"It's extremely important to make sure the reinforcing steel isn't attacked by salts," he says.
Corrosion of steel trusses in the collapsed bridge, the speculation goes, may have weakened it hastening its failure. The new freeway bridge when complete will be 10 lanes wide with room and strength for light rail.
Its life expectancy is 100 years.
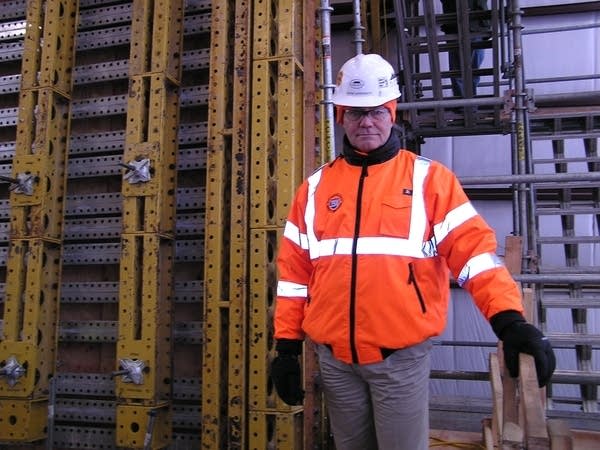
Unlike the bridge that collapsed the new span has redundancies which prevent a total failure, and the span can be repaired.
"The main load carrying members here, if there are failures it doesn't mean the entire bridge will collapse," Sanderson says. "The running surface can be ground off and replaced. If there are other problems there is provision for further post-tensioning which will help strengthen the bridge."
Post-tensioning works this way.
The new bridge will have 120 cast concrete and steel segments. The segments resemble in shape and size upside down A-frame houses, except that each one weighs up to 200 tons.
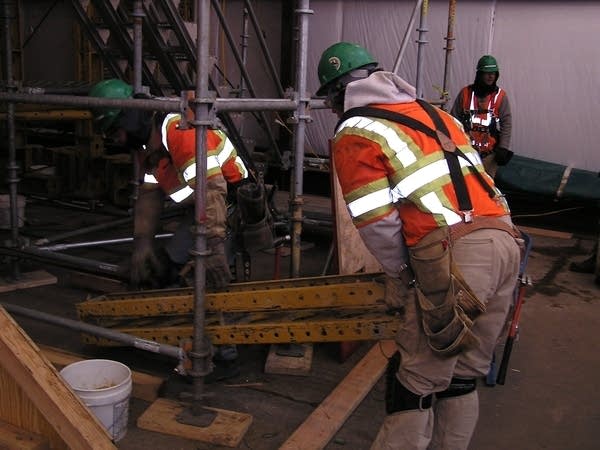
The top of each segment is a piece of the freeway deck, what vehicles drive on. Once the segments are poured and cured, they are skidded along the freeway roadbed, lifted by a crane and set in place end to end.
Then, like a multi-strand necklace of pearls, the 120 segments are strung together by 16 massive steel tendons. The tendons contain 27 strands of steel. Each strand has seven wires.
When all the segments are in place and the tendons are strung inside a jack is used to pull the tendons taut. The tendons are held in place by huge anchor blocks with wedges that prevent them from slipping back. The post-tensioning counteracts sagging and adds strength to the span. Thus the name of this particular kind of a bridge, Sanderson says.
"A pre-cast post tension concrete box girder bridge."
Peter Sanderson works for Flatiron Manson, the consortium that won the $234 million contract to build the new span.
He says a bit more than 30 percent of the bridge building work has been completed in 30 percent of the time allotted for the project - 437 days.
The bridge is scheduled to open December 24th.
"We're actually slightly ahead of schedule and we're happy with where we stand," he says.
Sanderson says a more normal construction period for a large project like the 1232 foot-long 35W span is two years or more. He says the bridge building activity reaches a peak this spring. As many as 30 workers a week, many from Minnesota, are being hired for the project. There'll be about 600 hundred on site working two shifts, seven days a week when warm weather returns.
Peter Sanderson helped build a bridge in Mumbai, India before this project. The weather consideration there wasn't cold, but humidity from the monsoon season. He says he's lost track of the number of bridges he's helped build but estimates its more than three dozen.
Every Saturday at 11 a.m. people can walk with Sanderson near the 35W bridge project as he explains what's going on. For many it's a once in a lifetime opportunity to hear from one of the world's most experienced engineers how a bridge is built.