Minnesota-based magnetics company scales up greener options
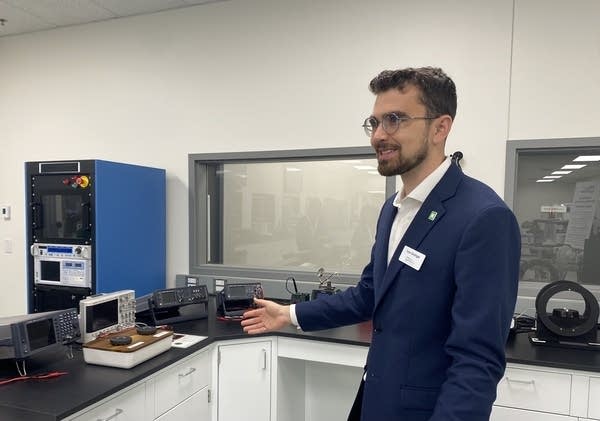
Go Deeper.
Create an account or log in to save stories.
Like this?
Thanks for liking this story! We have added it to a list of your favorite stories.
Minnesota-based Niron Magnetics has opened a commercial pilot plant in Minneapolis.
This plant will develop Niron’s “Clean Earth Magnets” that are developed from iron and nitrogen. The company says the magnets have the potential to be used in electric vehicles, wind turbines, audio products, and defense and weaponry.
Niron officials say the company’s magnets are produced in the U.S. through a process that is both the first and only one of its kind in the world. They’re an alternative to the vast majority of magnets that are manufactured in China from rare-earth materials that can require invasive new mining projects.
“This is truly a team effort on both legislative government level as well as, clearly, the Niron team level,” Sen. Amy Klobuchar said Thursday at an event for the ribbon-cutting of the new facility, where she was joined by company officials and other elected officials. “Scaling up your production capacity, investing in cutting edge new equipment, creating 60 good-paying jobs. And to think you've done this in just 10 short years, and I can’t wait to see what you’re going to do in the next 10 years.”
Turn Up Your Support
MPR News helps you turn down the noise and build shared understanding. Turn up your support for this public resource and keep trusted journalism accessible to all.
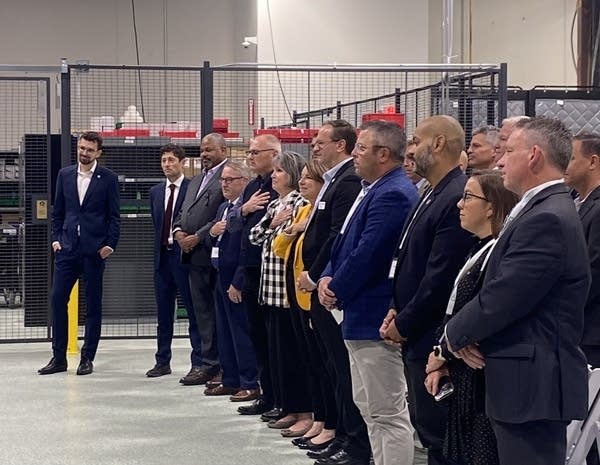
This 70,000 square-foot plant in Northeast Minneapolis has the capacity to manufacture more than five tons of magnets per year.
“It’s been a long journey to get to this point, from the early days when there were only about a dozen of us working in a small lab. Being able to progress the technology and scale it up step by step, and now we’re able to see it real, see it actually happen. We’re actually making materials, that’s what I am most excited about,” said Frank Johnson, Niron’s chief technical officer.
Niron’s process of producing a magnet starts with creating iron oxide powder. Iron oxide is also known as rust. Niron creates very fine particles of iron oxide that run through reactors that replace oxygen — oxide — with nitrogen. This then creates iron nitride powder, which is magnetic.
“We’re fighting at the national level to make sure Minnesota matters, and Niron is leading the charge,” Minnesota 8th District U.S. Rep. Pete Stauber said. “It does not happen without mining of our iron ore that makes our steel in this country. So this is a byproduct of the steel making.”
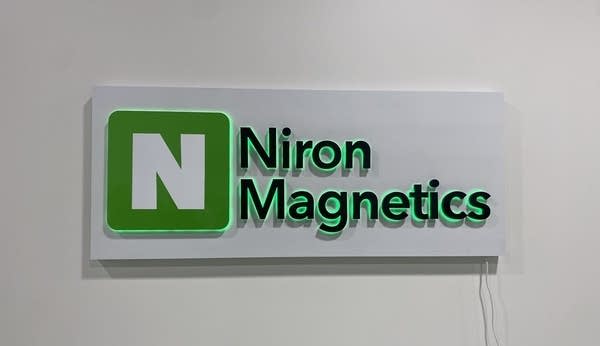
Iron nitride has been widely debated in science for decades, said Tom Grainger, Niron’s senior director of business development and investor relations. Research in 2011 at the University of Minnesota by Professor Jian-Ping Wang proved that iron nitride was as high-performance as some posited. This research was funded by the Department of Energy. Niron then developed a process to produce iron nitride.
“We were born in Minnesota,” Niron CEO Jonathan Rowntree said.
The byproducts of manufacturing the magnets are salt, water and water vapor.
“They’re cleaner to produce. They’re cleaner to recycle and they’re cleaner disposal. So it’s a win, win, win,” Minnesota 4th District U.S. Rep. Betty McCollum said.
Niron officials said the company’s magnets also allow the temperature of the products they are in, such as engines or motors, to remain more stable.
Rowntree said being able to offer magnets made in the U.S. is an attractive prospect for Niron’s customers.
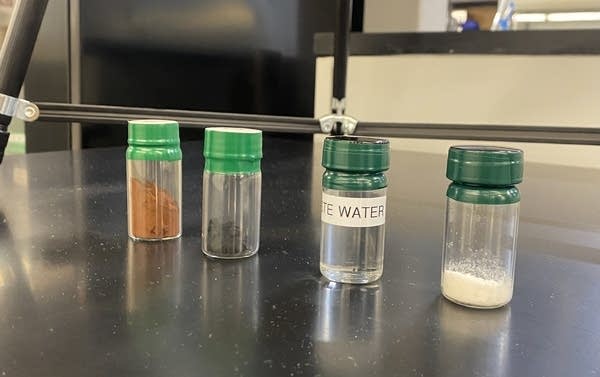
“I think reliability of supply definitely is what our customers are most concerned about. They also want to see more price stability," Rowntree said. “I think during COVID, that changed a lot of people’s perceptions on the world and the fragility of the planet.”
Rowntree also noted the more-plentiful supply of materials to make Niron’s magnets, compared to the rare-earth materials used in most other magnets.
“The amount of magnets needed will triple over the next 10 years. There’s only enough rare-earths in the ground today from the sites, the plants and mines that are operating to double that, so there’s going to be a very big shortfall in high performance permanent magnets, and that’s where Niron comes in,” Rowntree said.
The company’s customers so far include General Motors, Magna Powertrain, Samsung Electronics, Harman Audio, Allison Transmission, Volvo Cars and Western Digital.
Earlier this fall, Niron announced it had selected Sartell, near St. Cloud, for a larger manufacturing plant that will produce 1,500 tons of magnets per year.