Minnesota businesses get creative amid worker shortage
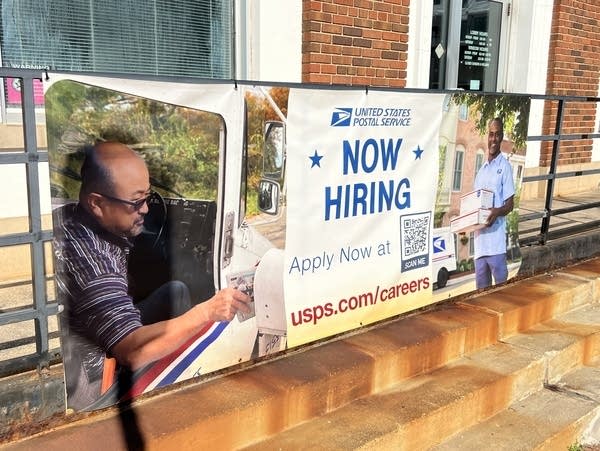
Go Deeper.
Create an account or log in to save stories.
Like this?
Thanks for liking this story! We have added it to a list of your favorite stories.
While many Minnesotans are eager to move on from the past few years of COVID-19 disruption, many businesses have yet to fully recover.
Take bars and restaurants, for example. Liz Rammer, the president and CEO of Hospitality Minnesota, the business association that represents restaurants, hotels, resorts and campgrounds, says bars and restaurants around the state continue to face big pandemic-related challenges.
“It's going to be a long term thing. You know, this is still going into 2023-2024,” Rammer said. “These businesses took on a ton of debt during COVID. They're trying to dig out.”
Rammer thinks reduced hours and other changes that many hospitality businesses made to survive the pandemic are here to stay.
Turn Up Your Support
MPR News helps you turn down the noise and build shared understanding. Turn up your support for this public resource and keep trusted journalism accessible to all.
“They discovered that they could be closed one or more days of the week, compress their hours of service,” Rammer said of some of the businesses she represents. “Many of those new kinds of practices have continued into the future.”
Minnesota’s unemployment rate is near a historic low. Although it ticked up slightly in December, it stands at 2.5 percent, a full point below the national rate. Many businesses are struggling to find people to fill vacant jobs.
Steve Grove, the commissioner of the Minnesota Department of Employment and Economic Development (DEED), said because of the tight labor market, some businesses are rethinking their relationship with workers and understanding the importance of embracing new workforce expectations.
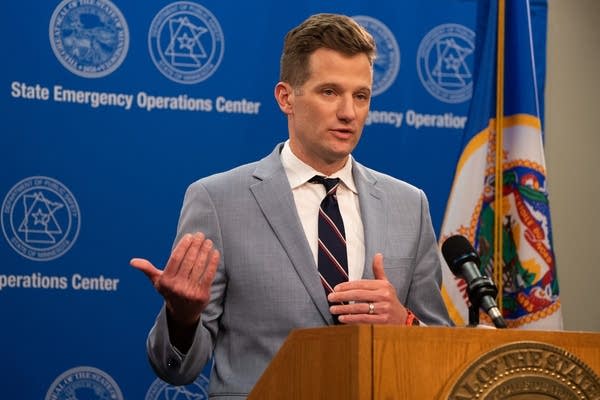
“Employers are trying some interesting things,” Grove said, including offering things like pet insurance, daycare and flexible scheduling.
“They're doing some really unique things in terms of the shifts that people can work,” Grove said.
Grove said the worker shortage is the “number one thing” holding back productivity among Minnesota businesses.
“If you don't have the workers to be on the factory floor, to be in the businesses that will help them grow,” Grove explained. “We're seeing companies just have to sit on orders.”
While the labor shortage is frustrating employers, it’s left prospective workers awash in opportunity.
“If you’re a job seeker in Minnesota and you're looking for work, this could be a great time to potentially find a promotion, find higher pay, find a better work culture, better benefits,” said Karl Amlie, who runs three Twin Cities employment agencies.
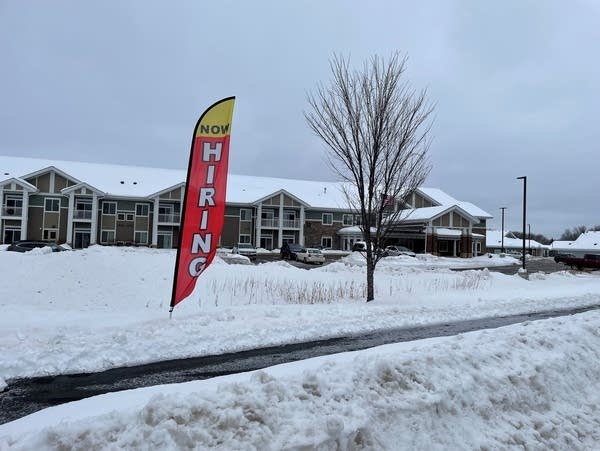
DEED Commissioner Grove said some businesses are also finding new ways to get work done without as many workers.
“We used to say, you know, we're all worried that the robots are coming to take our jobs,” Grove said. “And I think today we're like, we need more robots to come take our jobs.”
Jones Metal in Mankato is a company that’s been around for more than 75 years. It does custom metal fabrication. President & CEO Sarah Richards said automation is increasingly critical to the company’s productivity.
“We have 85 people right now that are producing as much as 125 people did 10 years ago,” Richards said, adding that automation at Jones Metal includes everything from office management software to robotic welders.
When companies think about automating tasks, they’d be wise to think beyond manual labor, Richards said.
“You have to sit down and sort of take inventory, take stock of what you're already doing,” said Richards, noting how voicemail eliminated the need to pay someone to answer the office phone and deliver messages.
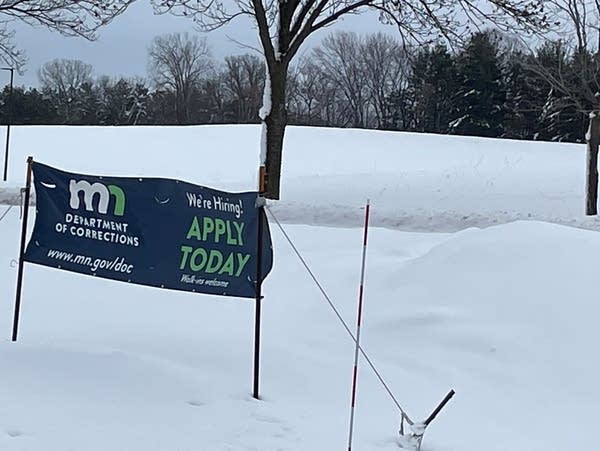
She also pointed to electronic timecards and other approaches that eliminate many tedious administrative tasks.
When it comes to actual robots, Richards said there can be incentives to help with the cost of sophisticated automation. Jones Metal got money from the Occupational Health and Safety Administration (OSHA) to buy a machine that wraps pallets for shipping. Now the process is safer and less expensive.
“The OSHA grant paid for half of the system,” Richards said. “The forklift drives the forks into it, and it automatically wraps the pallet on the front of the forks. Before it used to take two or three people to do that.”
Even with the efficiencies that come with expanding automation at Jones Metal, Richards said she’s convinced the most important thing any business can do to increase productivity is to partner with employees to make the best work environment.